Featured Posts
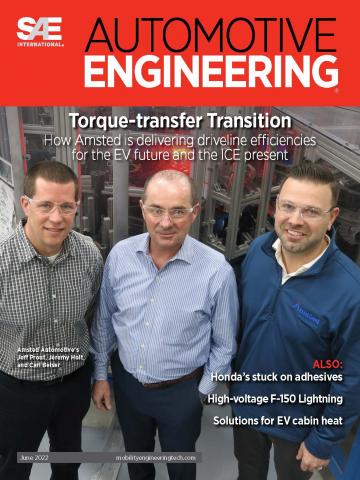
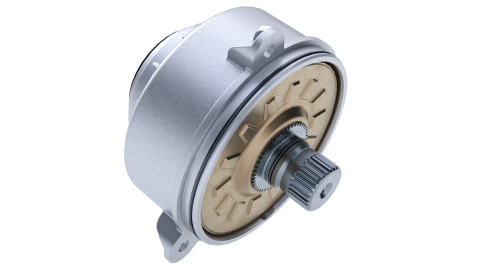
Something special happened in EV innovation when Burgess-Norton and Means Industries joined forces under the umbrella of Amsted Automotive.
By combining the design, engineering, and…
Novel Multi-Functional Clutch Technology for Seamless EV Driveline Disconnect and Improved Efficiency
Electric Vehicles (EV) drivetrain systems are being redefined—creating next-generation propulsion systems—as the EV market grows rapidly. This next generation of EV propulsion systems will need to be further optimized for function, efficiency, range and cost as the EV market scales up. This includes the need for new solutions to facilitate seamless eAWD disconnect with the ability to quickly and reliably shift between disconnected, forward propulsion, and regen or reverse modes. Design flexibility is also required for adaptability at multiple locations between the eMachine and wheels.
In addition to disconnects, next generation EV drivetrains will also require more sophisticated solutions for electronic park-lock, hill-hold and multi-speed shifting, combining the functions of historical ICE transmissions and drivelines. These technologies can be applied to EV passenger cars, light truck and commercial vehicles.
Means, an Amsted Automotive division, has developed controllable disconnect clutch and actuation technology with full disconnect and locking functions, plus the additional functionality for controlled bi-directional one-way-clutch operation. This technology, when applied to EV drivetrains, can provide novel and flexible system solutions for EV disconnects for both eAWD and primary electric drive unit (EDU) applications. The control and flexibility of this technology can also enable the same disconnect function and advantages for the primary EDU.
Additional capability can also be combined with multi-speed shift functions, hill-hold and park-lock features to create novel multi-functional clutch solutions for the next generation of EV drivetrains.
Something special happened in EV innovation when Burgess-Norton and Means Industries joined forces under the umbrella of Amsted Automotive.
Presentation - Novel Multi-Functional Clutch Technology for EV Driveline Disconnects
With the market growth of Electric Vehicles, EV drivetrain systems are in the process of being redefined and reinvented as part of the next generation of electric vehicle propulsion systems. Next generation EV propulsion systems will need to be further optimized for function, efficiency, range and cost as the EV markets scale up. This includes the need for new solutions to facilitate seamless eAWD disconnect with the ability to quickly and reliably shift between the power, regen and coasting modes. Design flexibility is also a requirement for adaptability at multiple locations between the eMachine and wheels.
In addition to disconnects, next generation EV drivetrains will also require more sophisticated solutions for electronic park-lock, hill-hold and multi-speed shifting, combining the functions of historical ICE transmissions and drivelines. These technologies can be applied to EV pass-cars, light truck and commercial vehicles.
Amsted Automotive has developed controllable disconnect clutch and actuation technology with full disconnect and locking functions, with the additional functionality for controlled bi-directional one-way-clutch operation. This technology when applied to EV drivetrains can provide novel and flexible system solutions for EV disconnects for both eAWD and primary drive EDU applications. The control and flexibility of this technology can also enable the same disconnect function and advantages for the primary drive EDU.
Additional capability can also be combined with multi-speed shift functions, hill-hold and park-lock features to create novel multi-functional clutch solutions for the next generation of EV drivetrains.
The first base disconnect for EV application was launched into production in 2021.
Click below to request a copy of the final presentation that was presented at CTI USA 2022.
Great Wall Motor (GWM) is the largest SUV manufacturer in China.
The Amsted Electro-Mechanical E-axle Disconnect Solution is the Missing Link in Efficient and High-Performing AWD and 4WD Electrified Propulsion
The demand for electric vehicle (EV) technology has seen exponential growth in the past several years. This is driven by many countries mandating electric propulsion as a high percentage of new vehicle sales in the very near future as well as customer demand. However, customer demand also dictates that a significant volume of vehicles need to be SUVs, crossovers and light-duty trucks with four-wheel-drive (4WD) and all-wheel-drive (AWD) capability – something that is not easily achieved with an electric drivetrain. Until now. MEANS Industries, an Amsted Automotive Group company, addresses this key drivetrain issue with the Dynamic Controllable Clutch, an Electro-Mechanical E-axle Disconnect system. More than a concept, this system is currently launching in production on a suite of 4WD electric vehicles.
This innovative disconnect system seamlessly engages and disengages front and rear electric drivetrains, enabling near instantaneous torque vectoring while also conserving energy and extending vehicle range.
“The Missing Link in Efficient and High-Performing AWD and 4WD Electrified Propulsion: The MEANS Industries Dynamic Controllable Clutch System – an Electro-Mechanical E-axle Disconnect Solution”
The Electro-Mechanical E-axle Disconnect system was necessary technology for EVs because traditional internal-combustion engine (ICE) powertrains were not engineered for the unique parameters and characteristics found in electric propulsion systems. These traditional clutches, such as hydraulic or even electrically actuated dog clutches, dramatically increase power losses and system mass. They also prove to be difficult to calibrate and are not the best solution for the instantaneous actuation desired by consumers.
While these two types of clutches can be integrated well into appropriate ICE-based powertrain systems, their shortcomings are compounded when used in an electric propulsion system – where hydraulics have been all but eliminated. EV powertrains favor mechatronic solutions that are easily calibrated and draw very little power for engagement and holding state. However, DCC technology uses electric actuation to create substantial packaging and system efficiencies by eliminating complex hydraulic systems.
DCC provides the benefits of latching in state without a constant power supply. Hydraulic control is eliminated, as are the associated costs and complexities. Even electrical requirements are reduced, as power is only consumed during state transition. Electro-Mechanical E-axle Disconnect application of the DCC provides efficient and unnoticeable engagement and disengagement of the front and rear electric drivetrain from the drive axles, while maintaining full on-road and off-road capability.
SMW Manufacturing is an international supplier of cold-formed components for heavy truck, mining, construction, and industrial markets.
If you’re shaping the conversation around eMobility trends and the future of drivetrain and powertrain technology, you’ll be in Berlin at this year’s CTI Symposium, November 30 to December 1
Demand for complex and electric vehicular components is exploding across the globe. The need for powder metal expertise has never been stronger.